A licensed electrical contractor calculates anticipated loads and installs the correct circuit breakers in the service panel according to local electrical codes. Important is that these calculations are based on information provided by the building’s owner or operator and must be accurate.
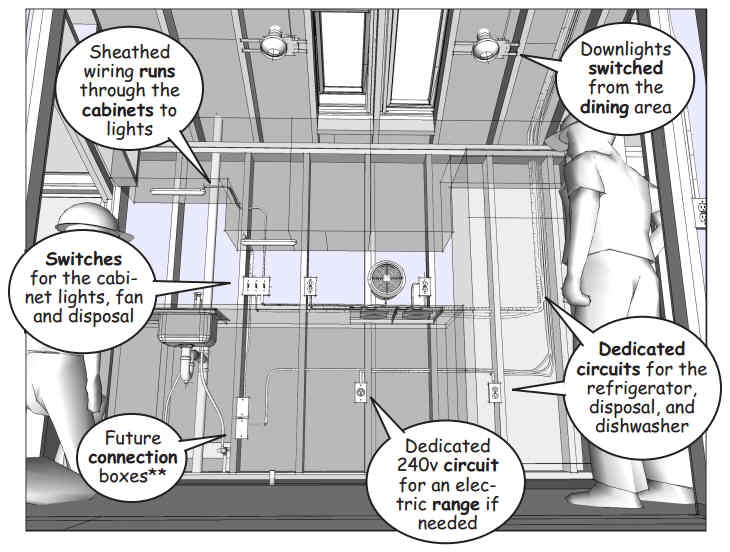
That said, most of the wiring for a residential structure is standard. Exceptions include computer and entertainment centers, kitchen and laundry areas, and local fire and safety requirements.
Sizing the system Wiring and breaker sizes vary with load requirements for each fixture and the potential accumulated loads for the branch circuits. The breakers use electromagnetic contacts or heat to sense overloads. This includes ground fault interrupters, arc faults, and high and low voltage fuses.

Service equipment like water heaters, HVAC systems, fans, and outside motor controllers require a single dedicated circuit to match manufacturer specifications.
Separate disconnect switches are placed at all inside and outside motor controllers to ensure technicians have local control of the power shut off.
Final review of the systemOnce all the wiring is in place and junction boxes are mounted and secured, the walls and ceiling are ready to receive insulation.

This work begins with a final check of the rough-in for the plumbing supply, drain and vents lines, the HVAC ducts, service lines, and the electrical wiring.
In some jurisdictions, authorization is required from a building inspector because once the insulation is in place, many systems will no longer be visible.
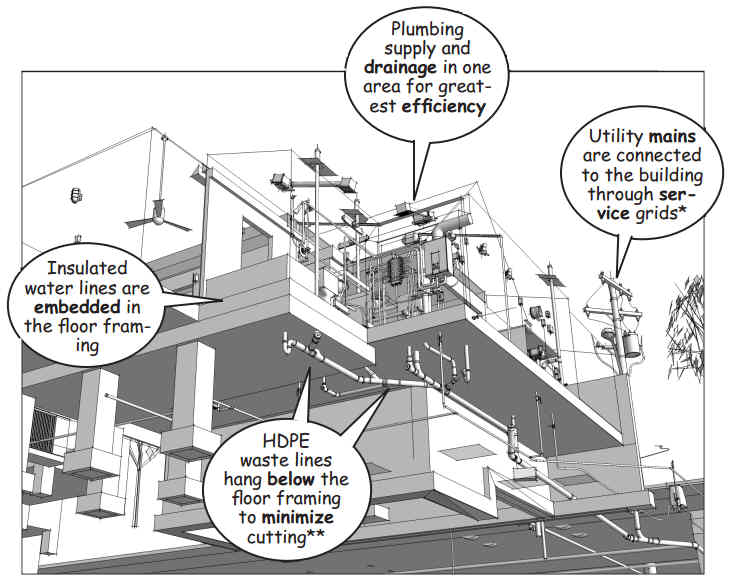
Items to check after the mechanical, electrical, and plumbing (MEP) rough-in are complete include:
• Interior walls inspected for proper framing sizes, tie downs, and connections
• Fire blocking as required at all frame penetrations
• Nail guards installed to protect wires and pipes at studs and joists
• Hangers, nailers, and supports for rails, fixtures, cabinets, piping, and wall fixtures
• Gate and back-flow valves in place for pressure testing
• Flood test drain pipes and pressure test water tubing and gas supply lines
• Gas and water shut off valves at all stub outs
• Vent ducts to outside air for dryer, bathrooms, and kitchen to prevent indoor air contamination
• Control wiring to fan coils and thermostats protected from damage
• Service feed and circuit breakers in place with wires run to all electrical boxes per local code
• Arc and ground fault receptacles ready for installation on circuits per local codes
• Non-metallic coated wiring of the appropriate gauge, stapled and protected
• Panel breakers mapped and labeled by the electrician at the panel
• Smoke and security detector wiring at the correct ceiling locations • Interior wall cavities swept clean and dry
.
(To be continued…)
---------------------------
The material presented in this series has been taken from our book, “How a House is Built: With 3D Construction Models” The book includes annotated illustrations, captioned text, videos, models, and the 2D Preliminaries.

..